Benefits of Creating a Digital Replica of Plant Using PDMS

In construction and engineering, many of the changes have taken place and many systems have changed. Well, the Plant Design management system is like the base of the engineering and construction industry. It is a strong platform for 3D modelling, design, and data management. However, the true capacity of PDMS is in its ability to serve as the base for creating a digital twin of a plant.
Here in this article, we are going to discuss the benefits of creating a digital replica of the plant using PDMS. So if you thinking of growing your career in this field, you can enroll in the PDMS Course. Taking this course will help you gain various benefits across the entire plant lifecycle. So let’s begin by discussing What is Digital Twin.
What is Digital Twin?
A digital twin is a virtual version of a real object, process, or system. It works just like the actual thing. By using data from sensors, the digital twin shows how the real object behaves and helps keep track of how it's working.
How to Create a Digital Twin with PDMS?
PDMS offers a strong and reliable platform for building a digital twin. So if you are looking to enroll in this course, it is necessary to know the PDMS Course Fees. This will help you decide to take the right course that fits your budget. Its advanced modelling capabilities give engineers the tools to:
Develop Detailed 3D Models
Create precise and intricate 3D models of the entire plant, capturing every component and their interconnections. This helps in visualizing the entire system and ensuring all parts are correctly placed.
Manage Engineering Data
Store, organize, and manage all engineering-related data, such as drawings, specifications, and material lists, in a central location. This makes it easier to access and maintain the data throughout the project lifecycle.
Integrate with Other Systems
Seamlessly integrate with various other systems, including process simulators, allowing for advanced simulations and thorough analyses. This integration ensures that the digital twin behaves as the real-world system would under different conditions.
Generate Reports and Documentation
Automatically produce a wide variety of reports and documents, including clash detection reports, material takeoffs, and isometric drawings. These tools are essential for verifying designs and ensuring the project meets all specifications and requirements.
Benefits of Creating a Digital Replica of the Plant Using PDMS
Here we have discussed the benefits of creating a Digital Replica of the plant using PDMS. So if you have taken the PDMS Course then you can implement these benefits into practice.
Improved Design and Engineering
The 3D model at the centre of the digital twin gives a very realistic view of the plant. This helps engineers spot potential problems, like pipes clashing or equipment interfering with each other, early in the design stage. By catching these issues early, it reduces the chances of expensive design changes and work being redone later in the project. The digital twin also helps everyone involved in the project—engineers, designers, contractors, and even clients—work together more easily. With a shared platform to view and interact with the plant model, communication improves, and misunderstandings are reduced. This ensures everyone is focused on the same goals.
Enhanced Construction and Commissioning
The digital twin gives useful information about how the plant can be built. By looking at the 3D model, construction teams can spot challenges like access problems or logistical issues and come up with better construction plans. This can help reduce delays and improve the overall project timeline. By addressing potential problems early through the digital twin, construction delays are minimized, keeping the project on track and preventing costly setbacks. The digital twin can also be used to find safety risks during the design and construction stages. By visualizing the plant in 3D, possible dangers like fall risks or electrical hazards can be seen and fixed. This helps create a safer working environment for everyone on the project.
Optimized Operations and Maintenance
By using real-time data from sensors, the digital twin can predict when equipment is likely to fail, so maintenance can be planned ahead of time. This helps avoid unexpected downtime, reduces maintenance costs, and keeps the plant running smoothly. The digital twin can also be used to improve how the plant operates by analyzing data and spotting areas that could be better. This could mean using less energy, producing more output, or improving overall performance.
Conclusion
From the above discussion, it can be said that creating a digital twin with PDMS is a powerful tool that can change how plants are designed, built, and operated. By offering a complete and precise model of the plant, the digital twin helps engineers and operators make smarter decisions, boost efficiency, and improve safety. As technology keeps advancing, the abilities of digital twins will only increase, bringing even more benefits throughout the plant’s lifecycle.
What's Your Reaction?
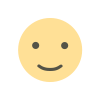
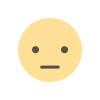
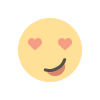

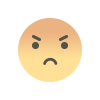
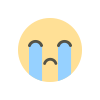
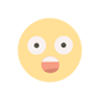