Den Herstellungsprozess von nahtlosen Stumpfschweißfittings aus SS 316/316L verstehen
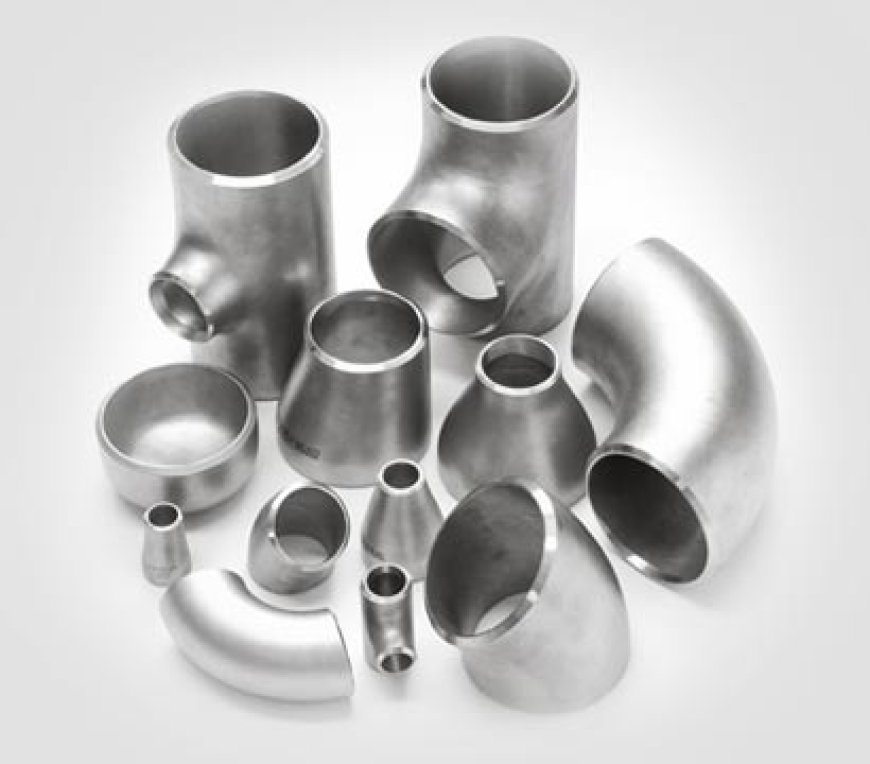
Herstellungsprozess von nahtlosen Stumpfschweißfittings aus SS 316/316L
Nahtlose Stumpfschweißfittings aus Edelstahl 316/316L spielen eine wesentliche Rolle in Rohrleitungssystemen, die in unterschiedlichen Industrien wie der chemischen, petrochemischen, pharmazeutischen und Lebensmittelbranche verwendet werden. Wegen ihrer hohen Korrosionsbeständigkeit, Robustheit und Beständigkeit gegen Abnutzung werden diese Fittings geschätzt. Um sicherzustellen, dass diese Fittings von höchster Qualität und Zuverlässigkeit sind, müssen sie im Rahmen eines hochpräzisen Herstellungsverfahrens produziert werden. Nachfolgend wird der Herstellungsprozess im Detail beschrieben.
Nahtlose Stumpfschweißfittings aus Edelstahl 316/316L sind grundlegende Teile von Rohrleitungssystemen, die in verschiedenen Branchen wie der Chemie-, Lebensmittel-, Pharma- sowie Öl- und Gasindustrie eingesetzt werden. Diese Fittings bieten eine dauerhafte, zuverlässige und korrosionsbeständige Verbindung zwischen Rohrleitungen. Um sicherzustellen, dass Haltbarkeit, Druckbeständigkeit und chemische Integrität höchsten Standards genügen, müssen bei der Herstellung dieser Fittings eine Reihe präziser Schritte durchgeführt und deren Qualität kontrolliert werden.
Nahtlose Stumpfschweißfittings aus Edelstahl (SS) 316/316L sind unverzichtbare Elemente in Rohrleitungssystemen diverser Industrien wie der chemischen, petrochemischen, Lebensmittelverarbeitung und Schifffahrt. Aufgrund ihrer hohen Korrosionsbeständigkeit, Festigkeit und Langlebigkeit werden diese Fittings geschätzt.
Diese Fittings werden in einem hochpräzisen Herstellungsprozess produziert, der mehrere technologische Schritte umfasst. Der gesamte Prozess – von der Auswahl des Materials über die Formgebung bis zur Endbearbeitung und Qualitätssicherung – wird in diesem Artikel detailliert beschrieben.
1. Materialauswahl
Der erste Schritt bei der Produktion nahtloser Stumpfschweißfittings besteht in der Wahl des Rohmaterials. Aufgrund seiner besseren Korrosionsbeständigkeit gegen Chloride und andere aggressive Medien wird Edelstahl 316/316L bevorzugt eingesetzt. SS 316L hat im Vergleich zu SS 316 einen geringeren Kohlenstoffgehalt, was eine bessere Schweißbarkeit und eine Reduzierung der Sensibilisierung für interkristalline Korrosion zur Folge hat.
2. Rohmaterialvorbereitung
Nahtlose Fittings werden aus einem massiven Edelstahl-Rohling oder einem nahtlosen Rohr hergestellt. Um sicherzustellen, dass diese Rohmaterialien den erforderlichen Spezifikationen entsprechen, werden sie gründlich geprüft. Bevor das Material in den Produktionsprozess überführt wird, werden seine mechanischen Eigenschaften, chemischen Zusammensetzung und Oberfläche überprüft.
3. Heißumformung (Hot Forming)
Das Rohmaterial wird in diesem Schritt erhitzt, um die notwendige Formgebung zu ermöglichen. Um eine gleichmäßige Verteilung des Materials und optimale mechanische Eigenschaften zu garantieren, wird das Material in einem kontrollierten Hochtemperaturofen erhitzt. Die Umgestaltung geschieht in der Regel durch eine der folgenden Methoden:
-
Extrusion: Ein massiver Stahlrohling wird unter hohem Druck durch eine Matrize gepresst, um die gewünschte Form zu erhalten.
-
Heißpressen: Hierbei wird ein vorgewärmtes Rohrstück in einer Matrize mit hohem Druck in die gewünschte Form gebracht.
-
Walzverfahren: Diese Methode wird für die Herstellung von nahtlosen Bögen und Reduzierstücken verwendet, indem das Material über eine formgebende Walze bewegt wird.
4. Wärmebehandlung
Das Material wird nach der Umformung einer Wärmebehandlung zugeführt, um Spannungen abzubauen und die mechanischen Eigenschaften zu optimieren. Dieser Vorgang, der als Lösungsglühen bezeichnet wird, findet in einem Ofen bei Temperaturen von 1.010 °C bis 1.120 °C statt. Danach wird eine rasche Abkühlung durchgeführt, um die Korrosionsbeständigkeit aufrechtzuerhalten und die Bildung von Karbidausscheidungen zu minimieren.
5. Kaltumformung (Cold Forming) und Nachbearbeitung
Zur Erhöhung der Maßgenauigkeit und zur Verbesserung der Oberflächenqualität werden viele Fittings kaltumgeformt. Die endgültige Form des Fittings wird durch Verfahren wie Ziehen, Walzen oder Pressen erreicht.
Um exakte Maße und eine makellose Oberfläche sicherzustellen, werden die Fittings nach der Kaltumformung mechanisch bearbeitet. Hierzu zählt das Drehen, Fräsen und Schleifen der Enden, um eine optimale Schweißbarkeit zu gewährleisten.
6. Beizen und Passivieren
Im Anschluss an die mechanische Bearbeitung wird eine chemische Behandlung durchgeführt, um Zunder, Oxidationen und andere Verunreinigungen zu beseitigen. Dies erfolgt durch Beizen in einer Säurelösung, die typischerweise Salpetersäure und Flusssäure enthält. Daraufhin erfolgt die Passivierung der Fittings mit dem Ziel, die Bildung einer schützenden Oxidschicht auf ihrer Oberfläche zu unterstützen, die die Korrosionsbeständigkeit zusätzlich erhöht.
7. Qualitätskontrolle und Prüfung
Jedes hergestellte Fitting muss strengen Qualitätskontrollen unterzogen werden, um sicherzustellen, dass es den Industriestandards entspricht. Die Prüfungen umfassen:
-
Visuelle Inspektion: Überprüfung auf Oberflächenfehler wie Risse, Porositäten oder Unregelmäßigkeiten.
-
Maßprüfung: Kontrolle der Abmessungen mit Messwerkzeugen, um sicherzustellen, dass die Fittings den Spezifikationen entsprechen.
-
Zerstörungsfreie Prüfungen (NDT): Dazu gehören Ultraschallprüfung (UT), Durchstrahlungsprüfung (RT) und Magnetpulverprüfung (MT), um innere oder äußere Fehler zu identifizieren.
-
Mechanische Prüfungen: Härte-, Zug- und Druckprüfungen, um die Festigkeitseigenschaften zu bestätigen.
-
Korrosionstests: Salzsprühtests oder interkristalline Korrosionstests, um die Korrosionsbeständigkeit sicherzustellen.
8. Endbearbeitung und Verpackung
Sobald die Qualitätsprüfung erfolgreich absolviert wurde, erfolgt eine Reinigung und Markierung der Fittings. Außerdem werden sie für den Versand vorbereitet. Die Kennzeichnung beinhaltet Angaben zur Materialqualität, zu den Abmessungen, zum Herstellungsdatum und zur Normkonformität (z. B. ASTM A403, ASME B16.9).
Um Transportschäden zu vermeiden, wird die Verpackung je nach Kundenanforderung in Holzkisten, Kartons oder Kunststoffverpackungen durchgeführt.
Fazit
Es handelt sich um einen komplizierten Prozess, der höchste Genauigkeit und rigorose Qualitätssicherungsmaßnahmen verlangt. Jeder Schritt, von der Auswahl des Materials über die Umformung und Wärmebehandlung bis zur Endbearbeitung und Prüfung, trägt dazu bei, ein Produkt mit herausragender Qualität und Langlebigkeit sicherzustellen. Diese Fittings sind in anspruchsvollen industriellen Anwendungen, die hohe Korrosionsbeständigkeit und mechanische Festigkeit erfordern, von entscheidender Bedeutung.
What's Your Reaction?
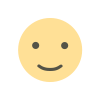
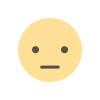
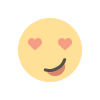

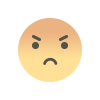
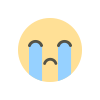
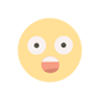